Feature
Automated exploration drill rigs: the next frontier
Exploration drill rigs are the next frontier of mining automation, but what innovation is emerging and is it happening fast enough? Heidi Vella reports.

Mining companies are looking to automate their exploration drill rigs to lower costs and increase process efficiency. Credit: Parilov / Shutterstock
Mineral exploration is often be considered to be a rudimentary process; one of hardcore geoscience, with prospectors poring over maps and collecting rock core samples using drilling technology that is, for the most part, still manually controlled.
In contrast, on the production side, autonomous drilling equipment is now standard, ranging from remote control, tele-remote and semi to completely autonomous.
Exploration drilling technology is therefore considered ripe for innovation, with numerous companies – from start-ups to stalwarts – vying to bring increased automation to the market. The benefits, they say, are myriad. Automated exploration drill rigs can improve safety by removing people from high-risk situations and requiring less driller intervention, helping ease acute labour shortages in the sector. Automation can also lower overall costs, given that wages, which can cost anything from $10,000–50,000 a day, are one of the main expenses occurred during drilling campaigns, in addition to potentially shorting time frames.
Anything involving automation is usually an opportunity for minimal interference, less risk, high efficiency and less carbon output.
What is more, as the energy transition rolls on, the demand for new mineral discoveries is projected to rise, with the International Energy Agency predicting 40-times more lithium and seven-times more rare earths potentially being needed by 2040 – a forecast barely compatible with the average 16.5 years it takes to identify and operationalise a new mine.
The technology is therefore welcomed by investors and prospectors alike. “Anything involving automation is usually an opportunity for minimal interference, less risk, high efficiency and less carbon output – all of which are aligned with the UN sustainable goals and net zero,” says Thomas Balogun, investment partner at Echo Eight Investments.
“You never say no to these kinds of technological advancements,” adds Yannis Tsitos, chair of the mining committee at Blue Lagoon Resources, which is developing the Dome Mountain Gold Project in British Columbia, Canada.
What have OEMs been waiting for?
The main problem identified by original equipment manufacturers (OEMs) is that automating rod handling for an exploration rig is considerably more complex than for a production drill rig.
Exploration requires drilling to much greater depths than the latter, meaning it is a more technical process. The drill usually requires access to multiple drill rods from outside the mast area, increasing the risk to the operator. Rod handling systems need to be ‘taught’ to start from a new position for every hole, says James Burris, marketing manager at drilling equipment and service provider Boart Longyear, which has been operating in the sector for 150 years.
The company has been shifting its rigs from manual handling to more autonomous and "drilling management focused" since 2016, when it launched the LF160 with hands-free rod handling, which mitigated heavy drill rod handling in the mast area. This was the "low hanging fruit" says product manager Zachary Strauss. The next step was automating inner tube handling, introduced with the LF160i. Once full of rock core, and especially if drilling at a steep angle, the inner tube can be difficult and risky to manually extract but automation now horizontally delivers tubes onto the core tray for disassembly and sample removal.

The LF160i undergoing testing in Arizona, USA. Credit: Boart Longyear
Building on this, the company is now testing a digested control panel for the LF160i in Chile and Australia, expected to be formally launched at the end of this year. Hydraulic actuated levers are omitted, and the panel moves from heavyweight steel to digital screens and joysticks. It requires no intervention from the driller’s assistant to align and cycle the rods or connect the hoist plugs when operating the loader. In addition, some tedious operations, such as positioning of the drill head for rod handling, can be automated.
The same advances are being made for underground rigs, but space constraints make the process trickier.
Strauss says automation in exploration drilling is not about the "big leaps", but the “incremental changes that take us to where we are trying to go”, which is to eventually have a drill operator manning several rigs at once, possibly remotely, using machine-collected data for quicker troubleshooting.
“I believe the industry is capable of this today, but the drilling conditions would determine viability or if it was economically advantageous,” he says. There are pros and cons, he adds; manual operation requires more attention from the operator, inducing fatigue and potential errors, but some steps can take longer when automated as they require cycling through more safety checks.
Customers will be monitoring the economic benefits closely. For example, professional geologist Eric Saderholm, managing director of exploration and co-founder of American Pacific Mining Corp, a Vancouver-headquartered precious and base metals developer, believes automation may not be a financially viable option for regional exploration programmes.
This is because companies can often be reluctant to replace fully functional equipment until they see it as a proven technology and cost-saving measure.
“Only then will it become a budget line item,” he says.
Most drilling equipment OEMs are on this path, however. Two years ago, Swedish manufacturer Epiroc collaborated with exploration drilling services provider Ausdrill to develop a rig with fully automated rod-handling, including some sequence automation for processes. The companies have said it was imperative to ensure the rod handler system was faster than the operators "otherwise they would simply continue doing the job manually".
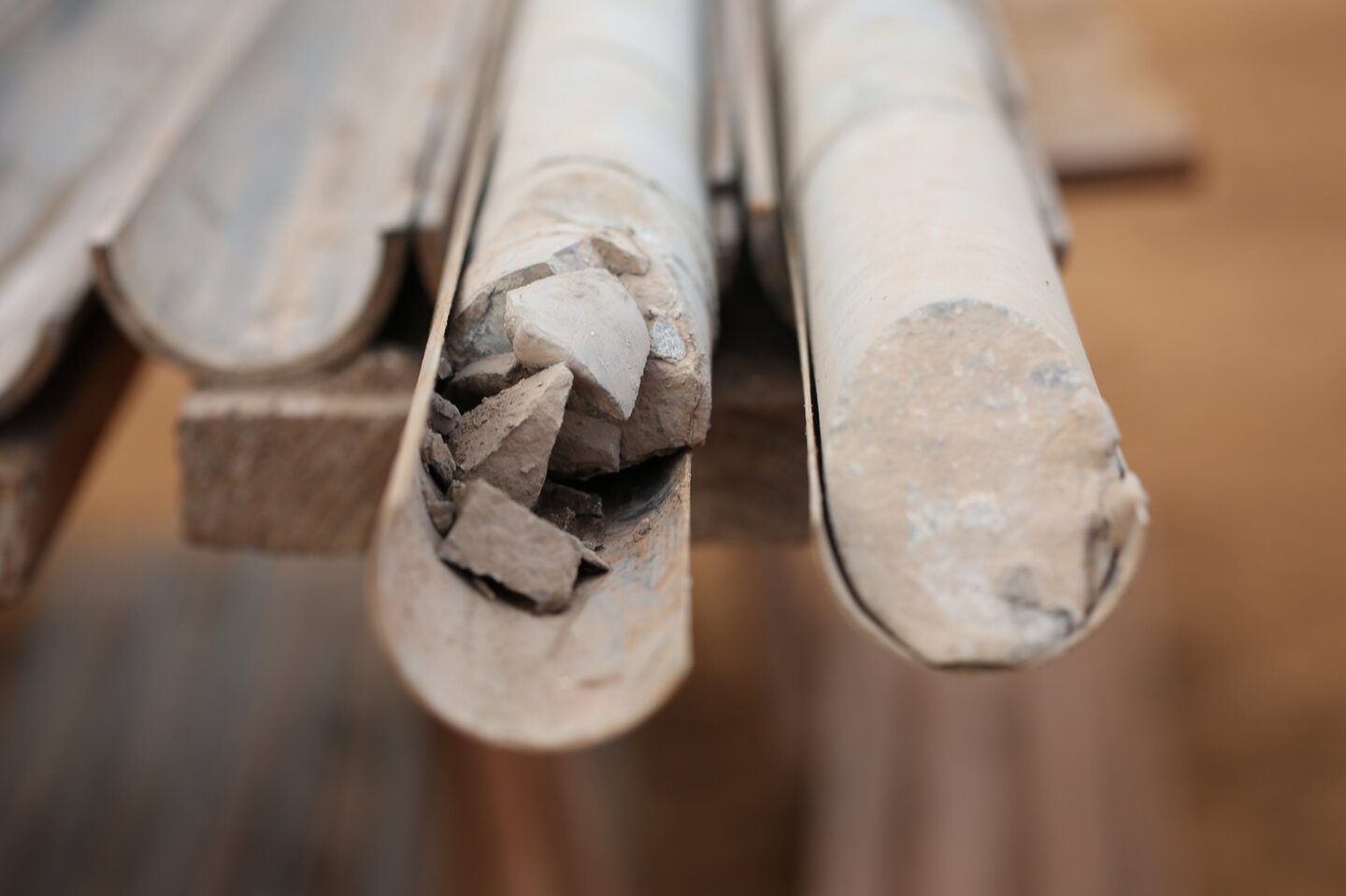
Core sample from the same mine site. Credit: Boart Longyear
Technology disrupters and industry conservatism
Along with the incumbents, lesser-known companies, spying an opportunity, are also laser-focused on implementing automation in exploration drilling.
Tribe Tech, for example, has partnered with Boart Longyear subsidiary Veracio to develop what it says is a first autonomous reverse circulation drill rig, the TTDS GC 700, which operates without personnel on the drilling pad. The company says the technology, reportedly being tested in Australia with McKay Drilling, can improve productivity and safety standards.
In addition, California-based Durin, established a year ago by Ted Feldmann, claims to be building remotely operated, semi-autonomous rigs that it plans to test at North American exploration projects. Last year it completed a pre-seed funding round with two investors.

Exploration drilling requires a level of precision and data interpretation that needs human oversight and insight.
Ioannis (Yannis) Tsitos, Chair of Blue Lagoon’s Mining Committee. Credit: Blue Lagoon Resources
Balogun believes new entrants will have trouble securing the hard capital needed to really get operations off the ground. “It is too much of a gamble for a start-up,” he says.
Also targeting this market is XtremeX Mining Technology, founded by experienced professionals from the oil and gas and mining industries. In January, it announced its drill rig featuring an automated control and hybrid power system. It will run a funded field trial with Ivanhoe Electric at the Santa Cruz copper project in Arizona, targeting depths of up to 2,000m by twinning historic holes. Under the agreement, Ivanhoe Electric secures exclusivity on three XMT rigs for contracts lasting up to five years.
Yet, despite Durin and XtremeX Mining Technology clearly targeting technology transfer from the oil and gas sector, Tsitos cautions that they are different processes.
“Exploration drilling requires a level of precision and data interpretation that needs human oversight and insight. You are trying to make every hole count in hitting a potential resource,” he explains.
“This differs in nature from AI-assisted drilling for oil and gas fields, where exploration holes are larger and targets less specific to find a resource and production potential.”
Inevitable innovation in autonomous drilling
Chris Hall, business development manager for Capital, a UK-based mining services company that is testing a digitised blast hole (D65) fleet in Tanzania, says automation, along with electrification, is the "holy grail" for the exploration industry.
“It is moving towards this [increased automation] and we hope eventually the drill rig could operate with limited intervention from the driller, offering efficiency and safety improvements,” he says.
Industry insiders agree full automation is inevitable.
“It is clear the market has spoken”, says Burris. “Eventually full automation will be a requirement. We witnessed an example of this when a major mining company dictated that all drilling contractors must use our LF160 and Rod Handling System.”
However, there is a debate about when, with customers more sceptical than the technology developers. Burris says fully autonomous drills are being tested but estimates they are 3–5 years from commerciality. Tsitos agrees that while AI-controlled drilling is coming to mining exploration, “wider implementation and industry acceptance can take at least ten to 15 years”.

Eric Saderholm, managing director of exploration at American Pacific, believes autonomous drilling can yield the greatest financial savings in large-scale mines. Credit: American Pacific
“Adaptation is coming, but the cost-effectiveness and productivity of autonomous drills in remote exploration settings are minimal compared to the savings that can be realised in large-scale mines,” adds Saderholm, whose company American Pacific operates in the western US with projects in Alaska, Montana and Nevada.
“Mining evolves at a slower pace than other industries,” he acknowledges, “but once automated drilling becomes a widely proven and cost-effective method, the dams of resistance will break and there will be a flood of adapters for the technology.”
As things stand, however, it is likely that in the near-to-medium term the industry will have more autonomous drilling technology to choose from, but it remains to be seen if it opts for the long-standing industry experts or the newer technology disrupters.