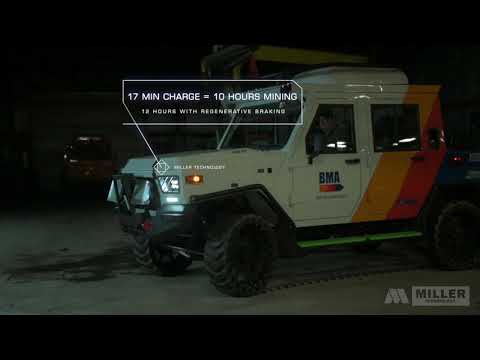
Miller Technology announces the sale and delivery of the first BEV Relays to BMA, part of mining major BHP, in Queensland, Australia.
This game changing LDV (Light Duty Vehicle) is capable of completing its bulk charge in less than 20 minutes, which provides enough range to complete a typical 10 hour mining shift. The regenerative braking can add up to 2 hours in a mine with optimised topology.
A 10 to 12 hours mining shift from a single 20 minutes charge is revolutionary.
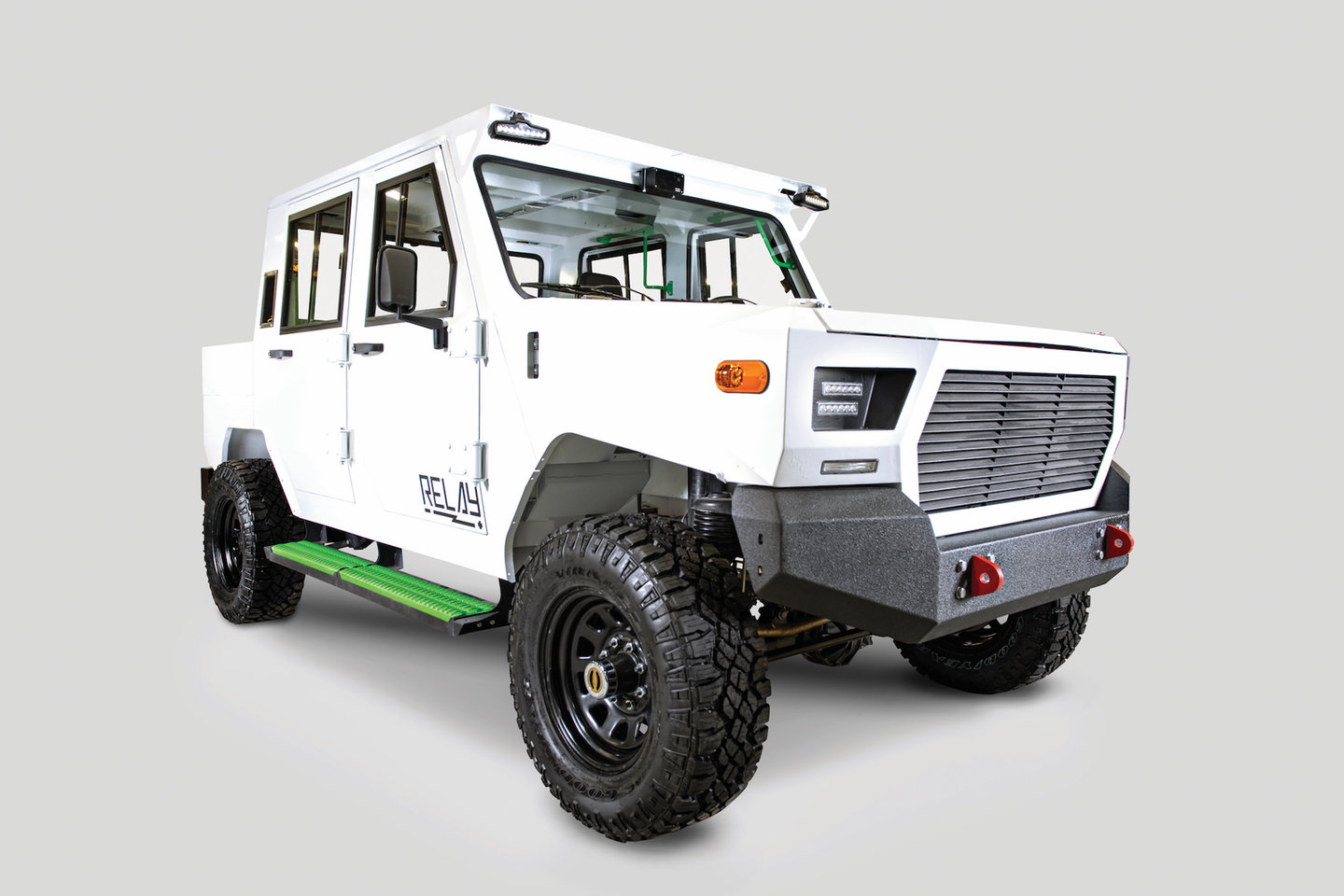

This is made possible by the advanced Battery Management System (BMS), which monitors battery temperature and its enclosed refrigeration temperature monitoring system keeps the temperature within the optimal narrow temperature range. The BMS responds instantly to varied demands while charging and in use helping the Relay to provide a 10 years battery life.
Unlike traditional BEV mining LDVs, which are modifications of donor vehicles, typically Toyota’s Land Cruiser, the ground up design of the Relay BEV has meant “everything that is mining” has been incorporated into every aspect of the design and production.
Miller Technology has invested over a decade of research and development into the Relay BEV focussing on serviceability, modularity with rugged design and construction. The Relay BEV was designed completely in-house by Miller Technology and utilizes an exceptionally efficient and robustly tested RESS (Rechargeable Energy Storage System). The system is rated for a maximum continuous 3C charging rate and maximum continuous discharge rate of 5C.
Utilising the CCS (Combined Charging Strategy) protocol via Combo-2 connection and NMC-G cells (Nickel Manganese Cobalt cathode and Graphite anode) offers charging with the most convenient and most widely adopted chargers worldwide.
Power is directed to a mid-mounted motor with dual drive output shafts providing 150kw (peak) to both front and rear differentials. With a drive shaft exiting each end of the electric motor the 4x4 system minimises moving parts and negates the need for a transfer case, capitalising on drivetrain reliability and power efficiencies.
The dual cab configuration can accommodate 4 mining equipped, work-ready adults comfortably and can carry a 2 ton payload. 1,550Nm of torque is available from the motor, providing enormous capability and offering the ability to offer the same drivetrain in the Miller Technology BEV Underground Grader.
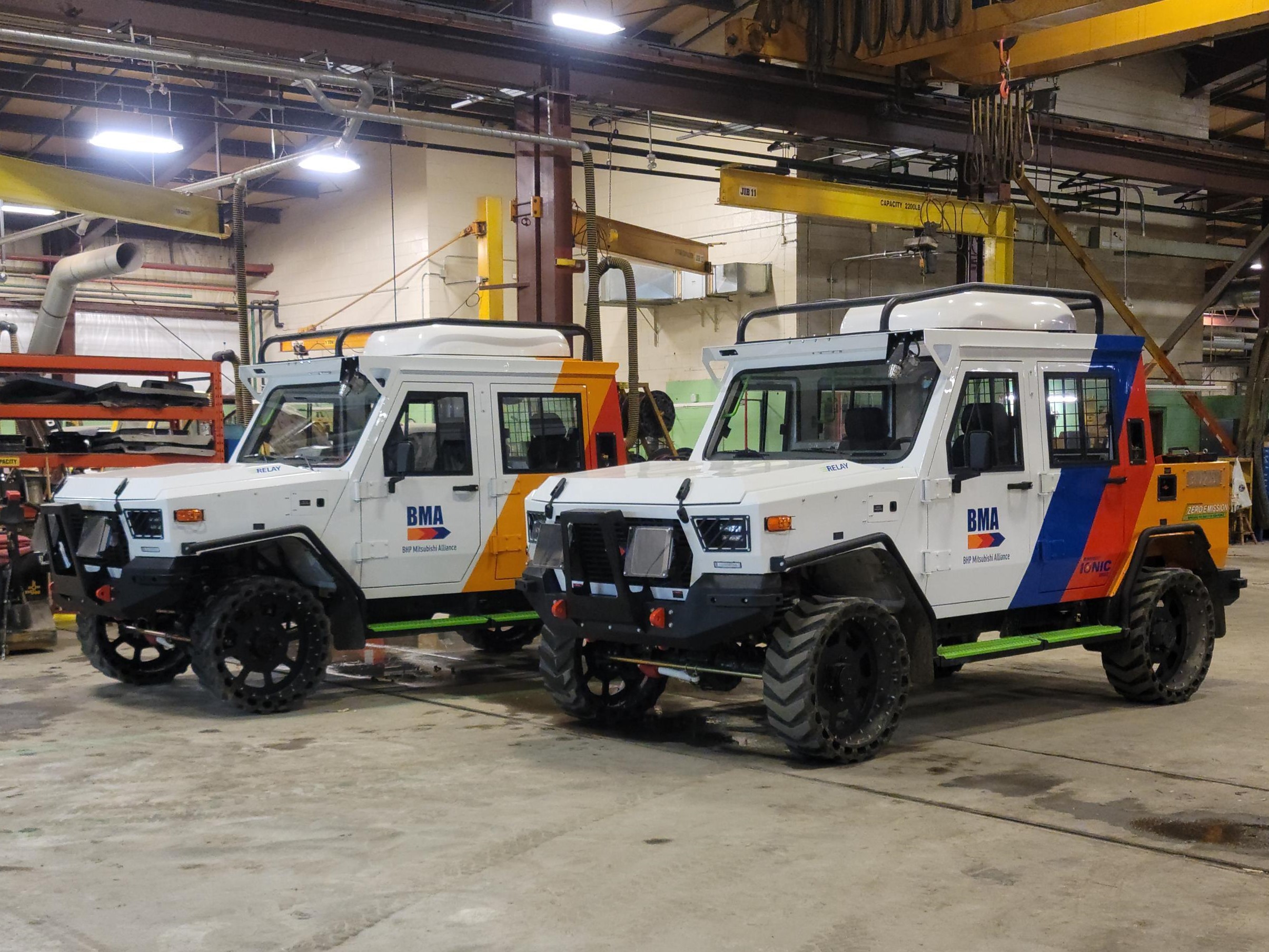
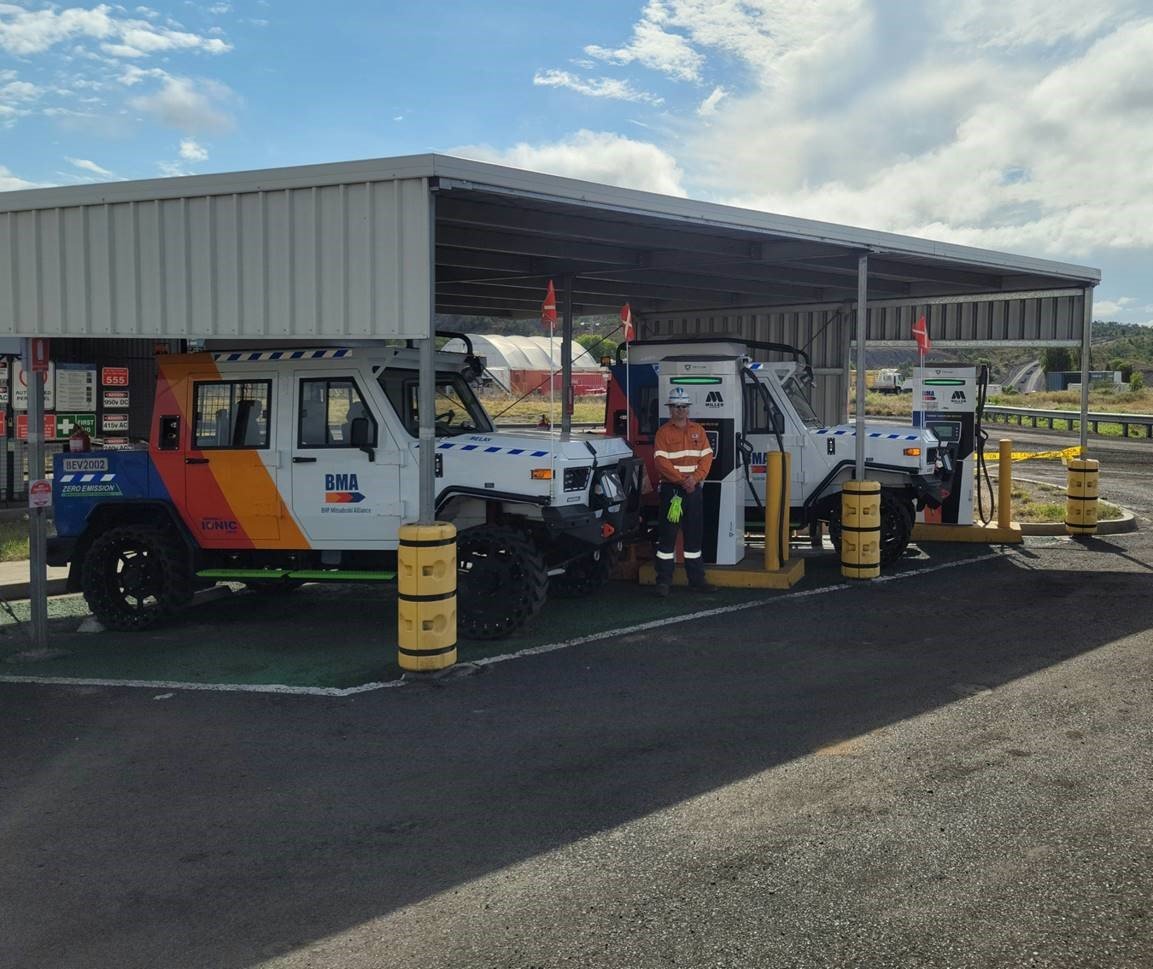
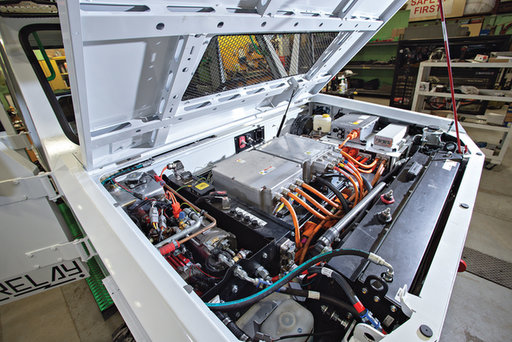
Being designed and purpose built specifically for mining from the ground up, a ROPS / FOPS Level 2 (Roll Over Protection Structure / Falling Object Protection Structure) is integrated into the cabin structure and operation is simple, with unparalleled comfort and exceptionally quiet running.
Telemetry diagnostics are data logged on board and transmitted to a control room through wi-fi or LTE networks. The data transfer is bidirectional, enabling onboard software to be updated remotely from a control room or mobile tablet.
“The technology in the Relay creates a game changing vehicle. The unique BMS battery management system and cooling/temperature monitoring process offers a vehicle at the top of its game, that is environmentally friendly and the safest, most efficient vehicle of its kind available today.”
- Paul Summers, Lead BEV Engineer
Contact Us
MILLER TECHNOLOGY PTY LIMITED
52 Bedarra St., Redland Bay
Queensland, Australia 4165
Email: admin@millertechnology.com
Web: www.millertechnology.com
GO TO TOP
MILLER TECHNOLOGY PTY LIMITED
52 Bedarra St., Redland Bay
Queensland, Australia 4165
Email: admin@millertechnology.com
Web: www.millertechnology.com
DELIVERY OF MILLER TECHNOLOGY
“RELAY” - MINING BEV (BATTERY ELECTRIC VEHICLE)
SCROLL DOWN
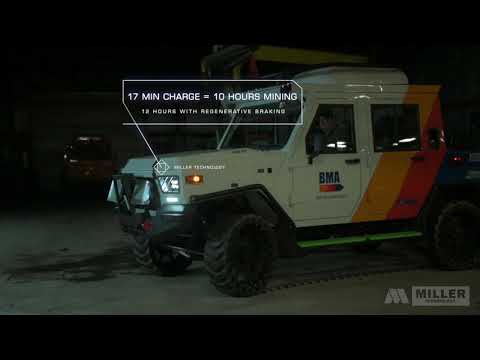
Miller Technology announces the sale and delivery of the first BEV Relays to BMA, part of mining major BHP, in Queensland, Australia.
This game changing LDV (Light Duty Vehicle) is capable of completing its bulk charge in less than 20 minutes, which provides enough range to complete a typical 10 hour mining shift. The regenerative braking can add up to 2 hours in a mine with optimised topology.
A 10 to 12 hours mining shift from a single 20 minutes charge is revolutionary.
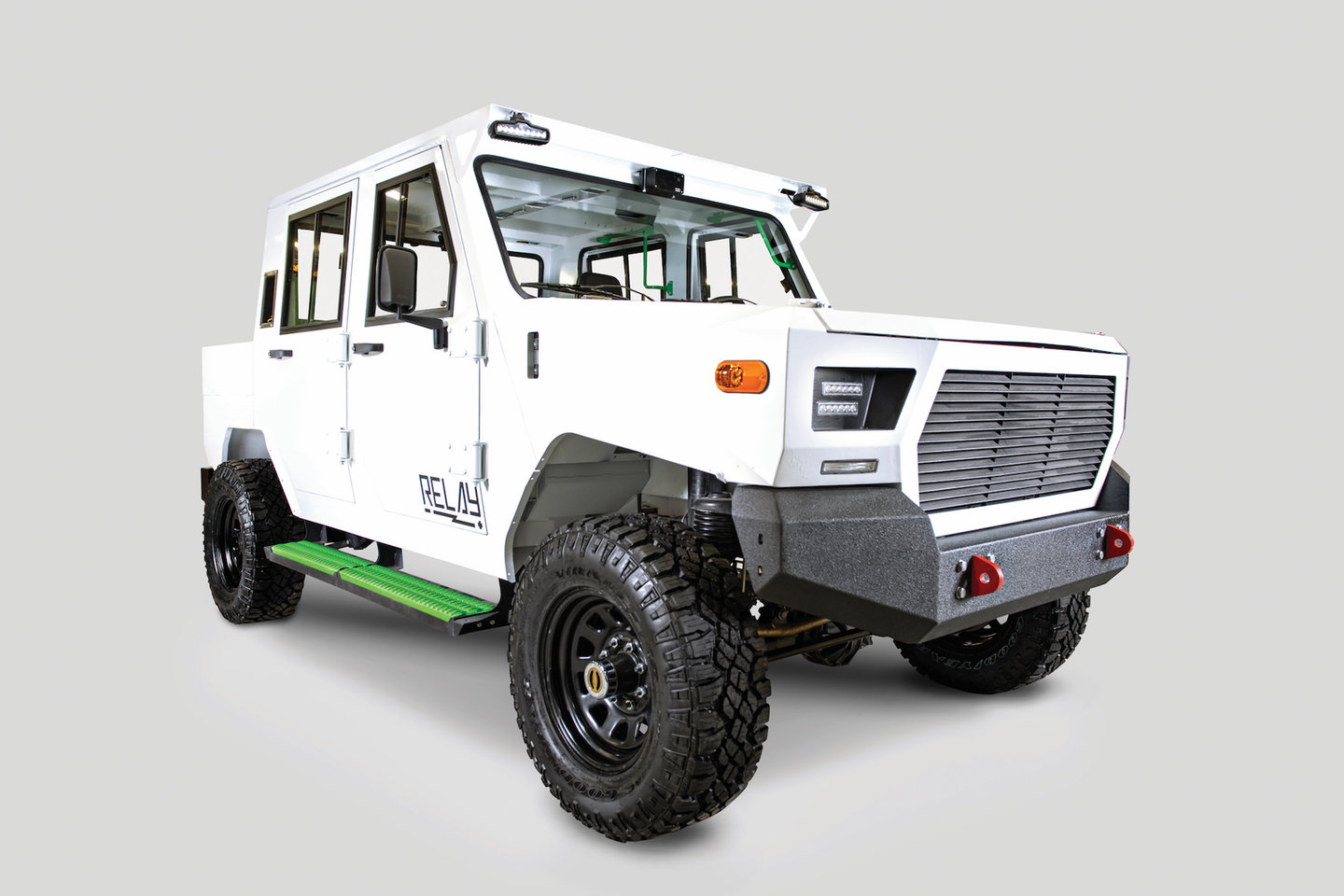

This is made possible by the advanced Battery Management System (BMS), which monitors battery temperature and its enclosed refrigeration temperature monitoring system keeps the temperature within the optimal narrow temperature range. The BMS responds instantly to varied demands while charging and in use helping the Relay to provide a 10 years battery life.
Unlike traditional BEV mining LDVs, which are modifications of donor vehicles, typically Toyota’s Land Cruiser, the ground up design of the Relay BEV has meant “everything that is mining” has been incorporated into every aspect of the design and production.
Miller Technology has invested over a decade of research and development into the Relay BEV focussing on serviceability, modularity with rugged design and construction. The Relay BEV was designed completely in-house by Miller Technology and utilizes an exceptionally efficient and robustly tested RESS (Rechargeable Energy Storage System). The system is rated for a maximum continuous 3C charging rate and maximum continuous discharge rate of 5C.
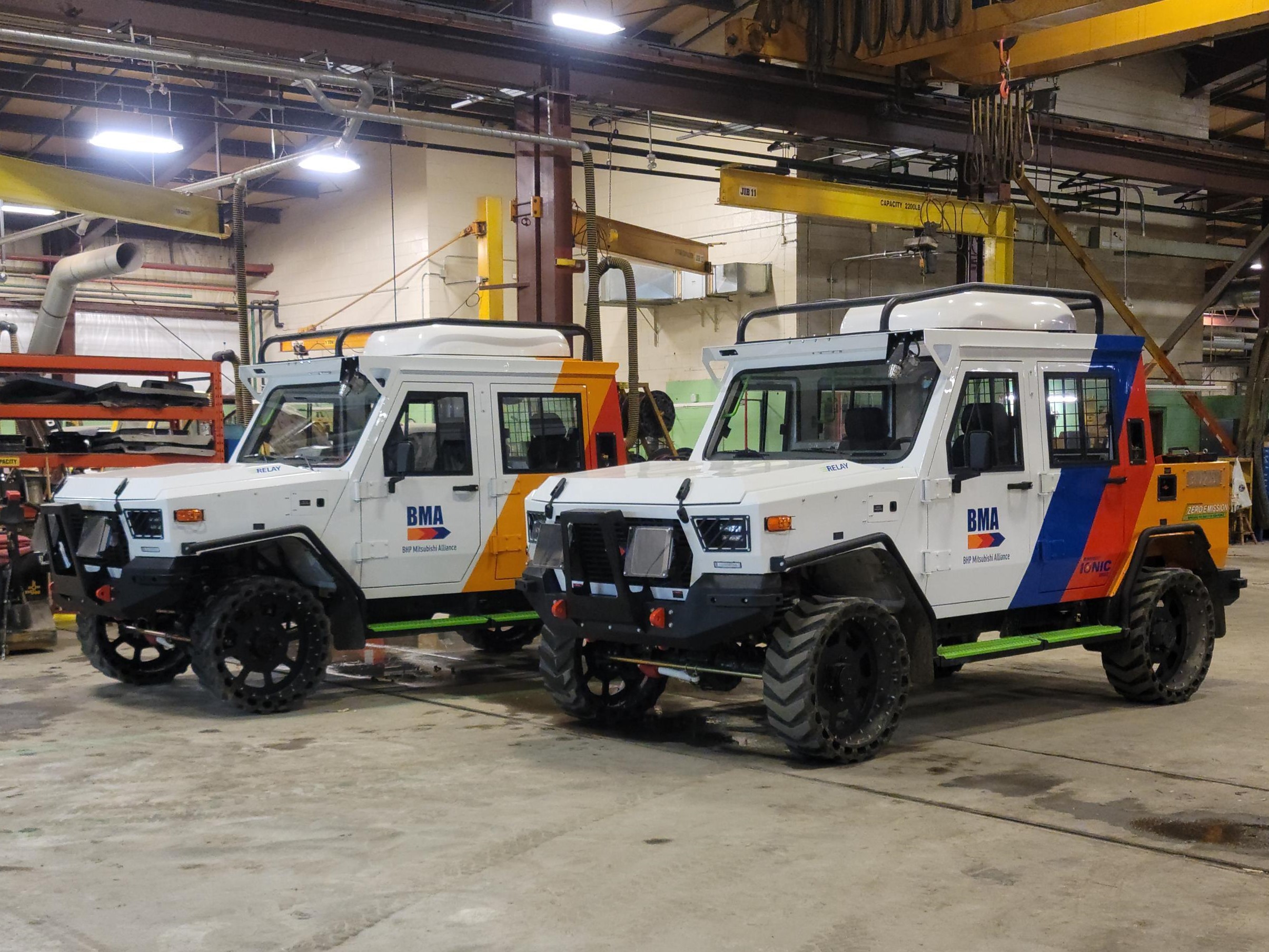
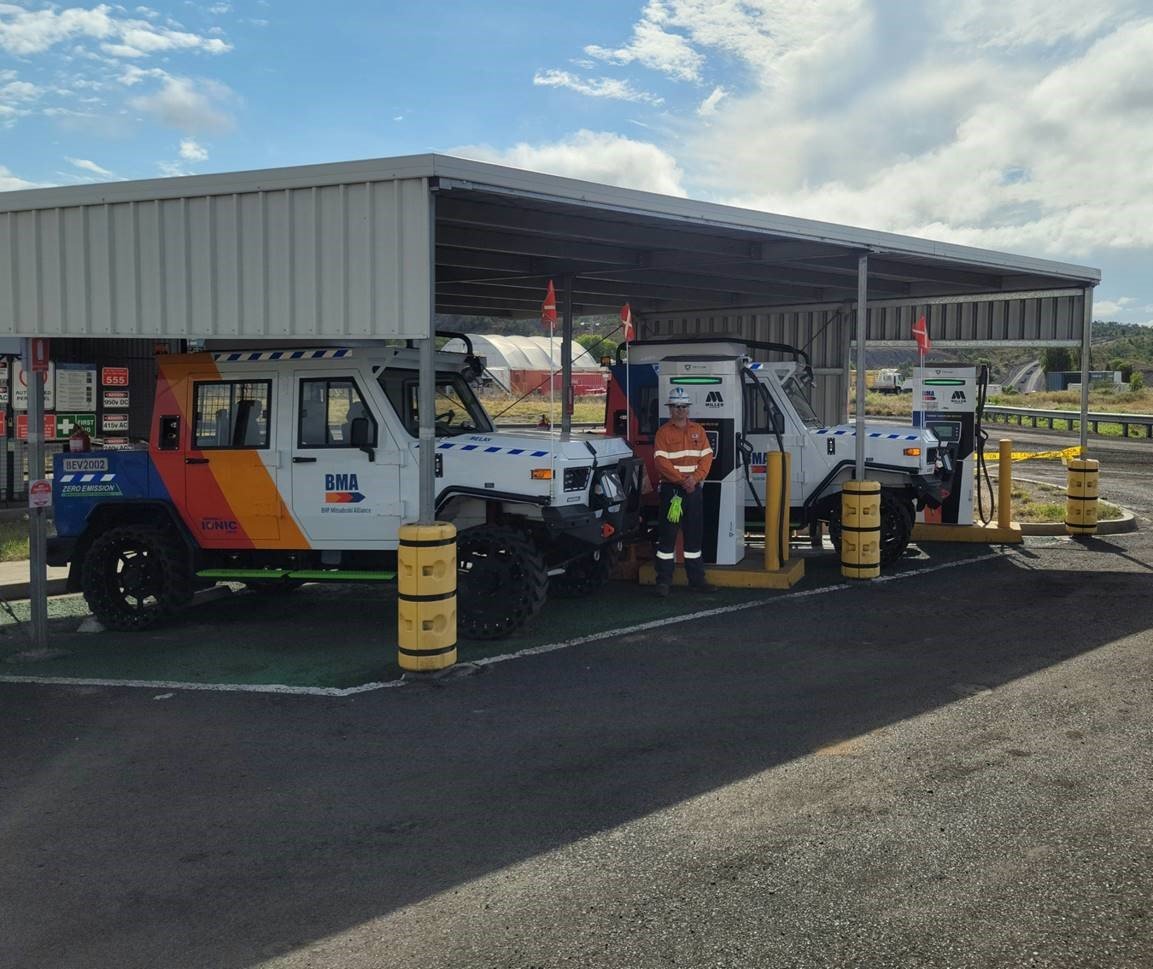
Utilising the CCS (Combined Charging Strategy) protocol via Combo-2 connection and NMC-G cells (Nickel Manganese Cobalt cathode and Graphite anode) offers charging with the most convenient and most widely adopted chargers worldwide.
Power is directed to a mid-mounted motor with dual drive output shafts providing 150kw (peak) to both front and rear differentials. With a drive shaft exiting each end of the electric motor the 4x4 system minimises moving parts and negates the need for a transfer case, capitalising on drivetrain reliability and power efficiencies.
The dual cab configuration can accommodate 4 mining equipped, work-ready adults comfortably and can carry a 2 ton payload. 1,550Nm of torque is available from the motor, providing enormous capability and offering the ability to offer the same drivetrain in the Miller Technology BEV Underground Grader.
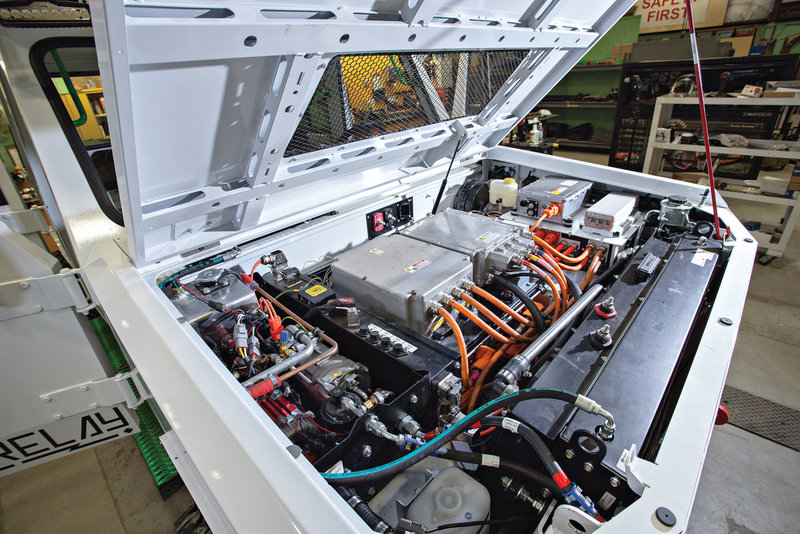
Being designed and purpose built specifically for mining from the ground up, a ROPS / FOPS Level 2 (Roll Over Protection Structure / Falling Object Protection Structure) is integrated into the cabin structure and operation is simple, with unparalleled comfort and exceptionally quiet running.
Telemetry diagnostics are data logged on board and transmitted to a control room through wi-fi or LTE networks. The data transfer is bidirectional, enabling onboard software to be updated remotely from a control room or mobile tablet.
“The technology in the Relay creates a game changing vehicle. The unique BMS battery management system and cooling/temperature monitoring process offers a vehicle at the top of its game, that is environmentally friendly and the safest, most efficient vehicle of its kind available today.”
- Paul Summers, Lead BEV Engineer