Company Insight
Sponsored by Vayeron
Enhanced efficiency and safety
Integrating Vayeron Smart Idler® technology in Atlas Energy Solutions’ Dune Express project.
Main image credit:
The bulk material handling sector, particularly in mining and logistics, faces recurring challenges, especially in maintaining conveyor systems. Atlas Energy Solutions, a leading provider of proppant logistics, has made a groundbreaking investment by incorporating Vayeron's Smart Idler® technology into its Dune Express Conveyor Project, a 67-kilometer conveyor system set to revolutionize proppant transport in the Permian Basin. This move is emblematic of Atlas’ commitment to leveraging cutting-edge technology to improve safety, operational efficiency, and environmental sustainability.
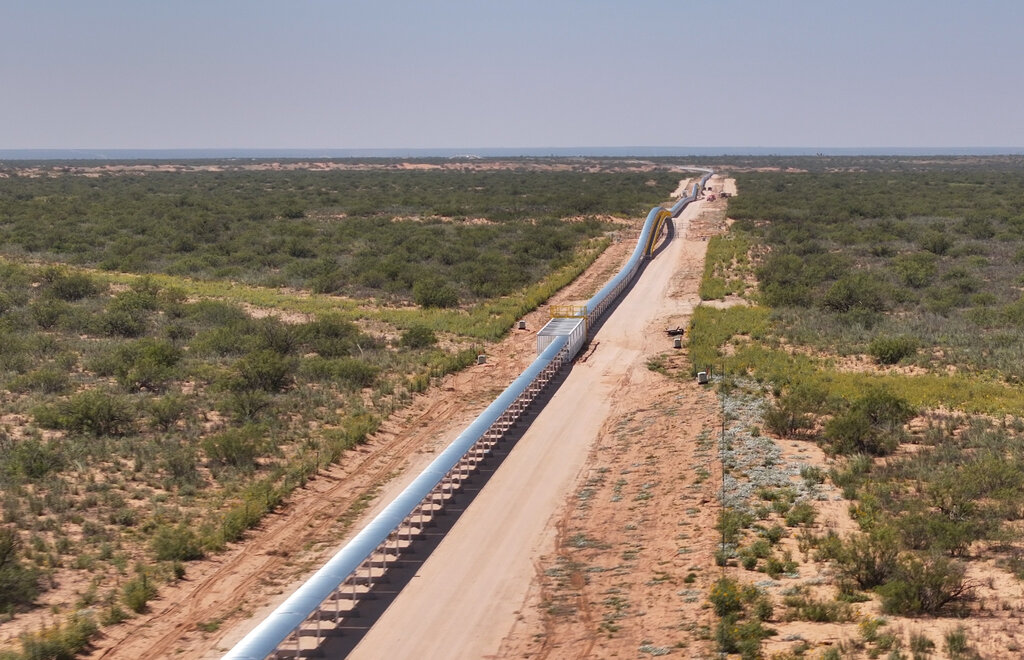
Caption. Credit:
The strategic importance of the Dune Express conveyor
Atlas Energy Solutions is deeply invested in the Dune Express project, which is expected to reduce the environmental and logistical impact of transporting proppant across West Texas. The project is a cornerstone of Atlas’ strategy to replace traditional trucking routes with an automated conveyor system, potentially reducing emissions and road traffic by up to 70%. With an expansive proppant demand in the Permian Basin and a focus on operational efficiency, Atlas is positioned to dominate the logistics market for hydraulic fracturing sand.
The Dune Express system, which spans 42 miles, requires close monitoring and maintenance of its nearly 70,000 rollers. This is where the integration of Vayeron's Smart Idler® technology offers unparalleled advantages in maintaining the operational integrity and efficiency of the conveyor.
Challenges of traditional conveyor systems
Traditional conveyor systems in mining and logistics industries often suffer from roller failure, a primary cause of downtime. Even seemingly minor issues, such as roller degradation, can lead to catastrophic failures, fires, and prolonged system outages. These events are not only costly—with downtime potentially costing operators like Atlas many thousands of dollars per hour—but could also present significant safety risks.
Given the scale and complexity of the Dune Express, traditional manual inspection methods are not feasible. Routine checks can be labour-intensive, prone to human error, and unable to detect early signs of wear or failure, which often leads to unanticipated breakdowns. For Atlas, avoiding these risks is essential to maintaining its commitment to operational excellence and high throughput logistics.
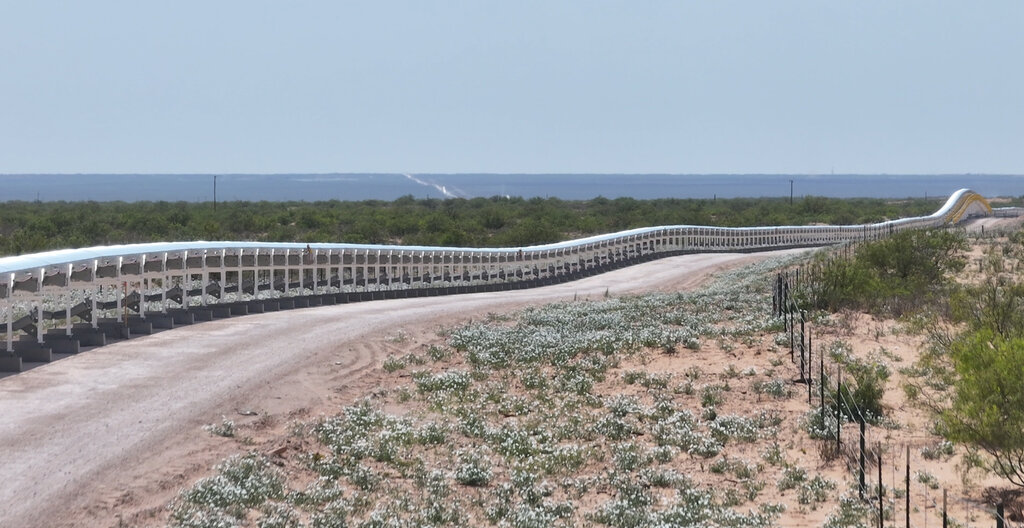
Caption. Credit:
Why Vayeron’s Smart Idler® technology is a game-changer
The decision to implement Vayeron’s Smart Idler® technology is rooted in its ability to autonomously monitor conveyor rollers in real-time. Smart Idler® integrates IoT sensors directly into conveyor rollers to gather data on temperature, vibration, and shell-wear. This data allows for predictive maintenance, identifying potential failures before they occur.
For Atlas, the Smart Idler® system provides several operational benefits:
- Proactive maintenance and predictive insights: The Smart Idler® detects wear patterns early, allowing Atlas to replace rollers before they cause unplanned outages. This shift from reactive to proactive maintenance means reduced downtime, higher conveyor availability, and more efficient resource allocation.
- Fire prevention: Roller failures, if left unchecked, can lead to heat buildup and sparks, which are significant fire hazards. The Smart Idler® mitigates this by constantly monitoring roller temperatures, thus preventing potential fires and enhancing workplace safety.
- Seamless integration with Atlas’s systems: The Smart Idler® works in tandem with Atlas’ roller change-out system, allowing for on-the-fly roller replacements without halting operations. This capability is critical for a system of the Dune Express' scale, where stopping the conveyor for manual repairs would result in substantial downtime.
Financial and environmental benefits for Atlas
The adoption of Smart Idler® not only enhances safety and operational efficiency but also delivers measurable financial benefits. Atlas’ second quarter financial results from 2024 underscore their focus on maintaining high profitability margins. By reducing unplanned downtime and extending the life cycle of conveyor rollers, the Smart Idler® system lowers maintenance costs and increases throughput. Moreover, the integration of this technology aligns with Atlas’ broader goals of sustainability, reducing the need for excessive roller replacements and contributing to a lower carbon footprint.
Atlas Energy Solutions has consistently demonstrated a forward-thinking approach to leveraging advanced technologies for better operational performance. The Dune Express project, when fully operational, will solidify Atlas as a leader in efficient proppant transport. Smart Idler® plays an integral role in this, ensuring that the conveyor operates at peak efficiency while minimizing environmental impact and maximizing safety.
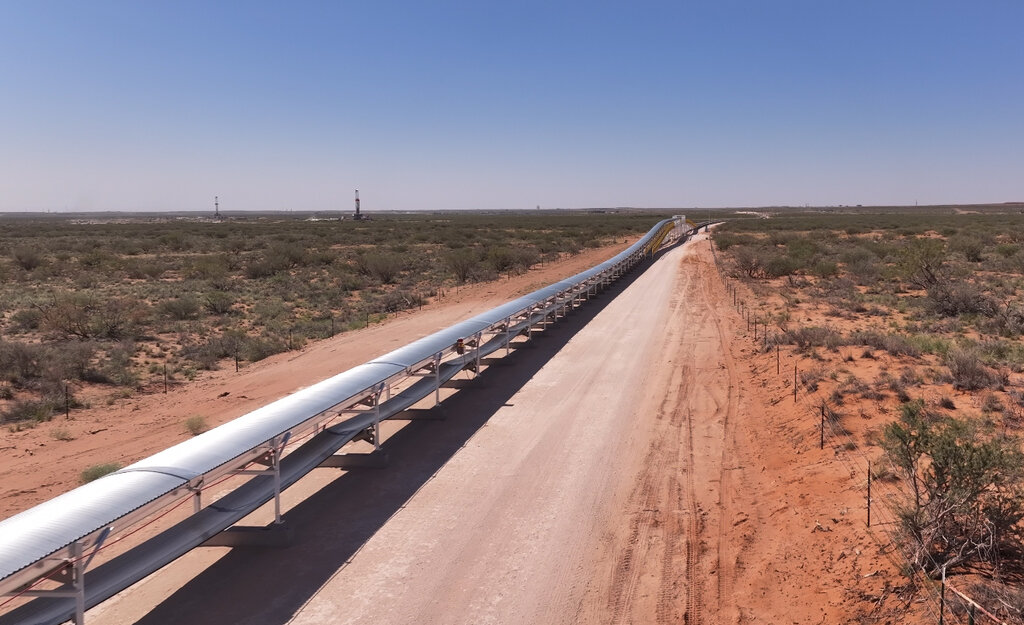
Caption. Credit:
Conclusion
Incorporating Vayeron’s Smart Idler® technology into the Dune Express Conveyor Project exemplifies Atlas Energy Solutions’ commitment to innovation, safety, and operational excellence. By utilizing real-time monitoring and predictive maintenance, Atlas is positioning itself at the forefront of proppant logistics while safeguarding its investment in one of the most ambitious conveyor projects in the industry. With the Smart Idler® technology in place, Atlas can confidently reduce risks associated with roller failures, minimize costly downtimes, and contribute to a more sustainable and efficient operation.
This partnership between Atlas and Vayeron represents not just the future of conveyor monitoring but a strategic investment in the future of energy logistics in the Permian Basin.
Contact information
Vayeron
L2, Building 4, 92 Sydney St CQ University,
Mackay, QLD, Australia
Tel.: +61 1800 404 160
Email: info@vayeron.com.au
Web: www.vayeron.com