COMPANY INSIGHT
Sponsored by IDCON INC
Your Maintenance Debt Dictates Your Maintenance Cost
Appreciation of the effect of changing regulations enables mine operators to proactively assess and respond to their relative exposure. A proactive response enables the operator to retain control of change processes in advance of a regulatory direction enforcing the change, the resource demand and the timeframe.
By way of example, Aspect Environmental looks at the requirements of the NSW Mining Amendment (Standard Conditions of Mining Leases – Rehabilitation) Regulation 2020 and how operators can respond and retain process control.
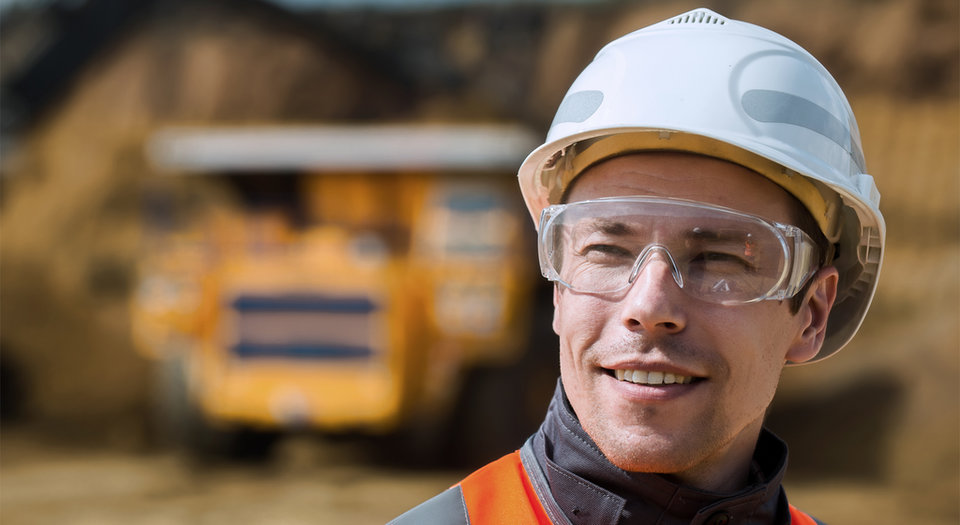
M
ost maintenance managers feel the pressure of lowering maintenance costs while improving reliability. Annual maintenance costs have a strong correlation to how well basic work processes such as planning, scheduling, and preventive maintenance are executed in our mines. But another often forgotten factor that heavily influences maintenance costs is your existing “maintenance debt”.
IDCON’s definition of maintenance debt is the total cost to repair all equipment in need of repair. This equation doesn’t include improvements, only the costs for repair of existing equipment problems. It is important to remember that the maintenance debt is the sum of all repairs, because a valid maintenance repair job can never be avoided only delayed. If you think about that statement, and find it to be true, you will also arrive to the conclusion that you have to pay the maintenance debt, there is no other alternative.
A valid repair can never be avoided, only delayed.
If you think about the statement above, and find it to be true, you will come to the conclusion that you have to pay the maintenance debt.
Here’s a scenario:
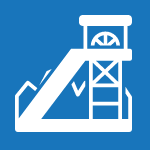
For 10 years, “Efficient Mine” has kept up, and continuously improved, its preventive maintenance (PM), planning and scheduling and other key work processes. They have maximized their resources and managed their maintenance budget, retaining a maintenance debt of $300,000.
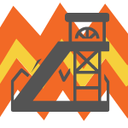
Chaotic, on the other hand, has spent 10 years working reactively, unable to keep up with repairs. They need to spend $5 million to make all necessary repairs.
Their annual maintenance budgets are identical, and they have the same resources and 100 internal craftspeople. Efficient Mine’s reliability is at 90% and Chaotic’s is at 75%.
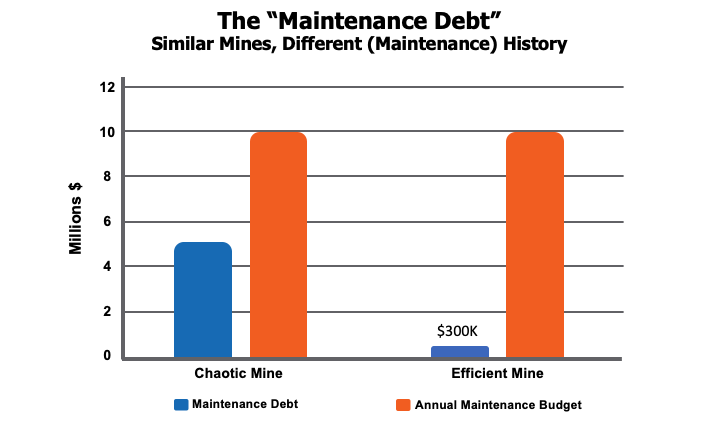
Figure 1: It will cost Chaotic Mine $4.7M and 31 additional craftspeople for 1 year and 1.41 M in materials to catch up to Efficient Mine's results. This theory only works if Chaotic manages to perform as well as Efficient in regard to planning, scheduling, PM and other maintenance and reliability work processes.
The Wrong Reaction
Many mines in Chaotic’s situation will reduce the maintenance budget in an effort to minimize the expenses and show better results. The problem? The results will only last for a short time. You can never avoid a valid repair work order! It’s also more cost effective to repair sooner than later, often by a ration 1:3 -1:9.
So, what’s the price tag for Chaotic to reach the same reliability as Efficient? It will cost roughly $4.7million in maintenance hours and material. But, for the theory to work long term, they must implement efficient work processes to maintain that level of reliability.
Let’s assume that 30% of Chaotic’s maintenance debt ($1.5 M) is material, and one maintenance hour costs about $60 USD. The total cost to get to Chaotic’s reliability will be 58,333 maintenance hours + $1.5 million in materials. Breaking it down further: 31 full-time employees working a full year (58,333 hours and 1,880hrs/worker/year) + material.
The repairs could be done over a longer period of time since it may be hard to plan and schedule for that number of people and other factors that play a role. One could, for example, add 10 additional people for 3 years. If Chaotic gets its PM, planning and scheduling implemented, the additional people will be a temporary.
A good idea may be to match the incoming “temporary addition” with natural attrition in the work force, in order to keep a trained work force in place.
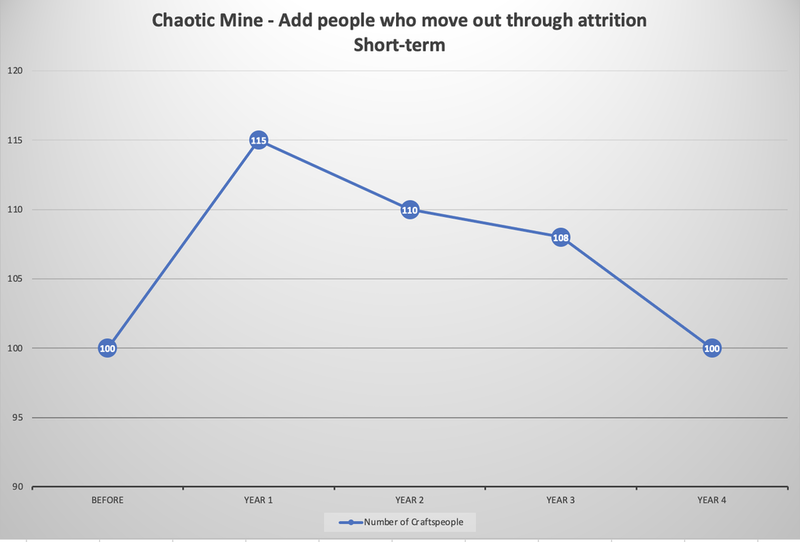
Figure 2: Chaotic Mine needs 31 effort years to reduce the maintenance debt. They decided to hire 10 additional people over 3 years. An alternate idea is to add 15 people to the regular workforce and let attrition reduce back down to 100 over 3 years
Analyzing Maintenance Debt
When IDCON works with clients to improve reliability and maintenance, we take a critical look the work processes in place, how finances are reported and past history. Our clients must understand the costs and time needed to improve reliability.
We review a portion of the equipment with knowledgeable personnel and analyze the maintenance backlog. This gives a rough estimate of the current maintenance debt. While an exact sum is best, the most important thing is to identify if the debt small, medium, or large.
Here’s our approach
- A work process review. How do existing preventative maintenance, priorities, planning, scheduling, and basic material management effect the maintenance cost?
- If they have multiple sites, we compare the maintenance costs. We verify that similar items are included in the maintenance cost. Read our Client Case Study
- Identify the size of the ”maintenance debt.”
- Document an improvement plan
- Implementation
- Follow up
The benefit of adding an analysis of the maintenance debt is that you get approximate figures of work hours and costs needed to improve.
But in reality, in order to improve reliability, Corporate management must accept that identified repairs must be done.
I hope these thoughts and example can help you get a grip on maintenance debt to improve reliability in your mine. For more information read the article “How to reduce maintenance cost the right way”.